In the stone processing industry, marble crushing equipment and stone crushing equipment are core production tools that directly affect production efficiency, finished product quality and operating costs. This article will introduce the types, working principles, selection techniques and industry applications of stone crushing equipment in detail to help you choose the most suitable crushing solution.
1. Main types of stone crushing equipment
Based on the crushing principle and applicable scenarios, common stone crushing equipment can be divided into the following categories:
1.1 Jaw crusher (coarse crushing equipment)
• Applicable materials: marble, granite, basalt and other hard stones
• Working principle: crushing stones through the extrusion movement of the movable jaw and the fixed jaw
• Advantages: simple structure, easy maintenance, large processing capacity, suitable for primary crushing
• Typical applications: mining, sand and gravel aggregate production line
1.2 Cone crusher (medium and fine crushing equipment)
• Applicable materials: high hardness stone (such as granite, quartz stone)
• Working principle: use hydraulic or spring system to achieve lamination crushing
• Advantages: high crushing ratio, good finished product particle shape, strong wear resistance
• Typical applications: highway, railway ballast production
1.3 Impact crusher (medium and fine crushing equipment)
• Applicable materials: medium hardness stone (such as limestone, marble)
• Working principle: The high-speed rotating rotor hits the stone to achieve impact crushing
• Advantages: The finished product has uniform particle shape and low energy consumption
• Typical applications: construction aggregate, machine-made sand production
1.4 Hammer crusher (suitable for soft stone)
• Applicable materials: limestone, shale and other low-hardness stones
• Working principle: The high-speed rotating hammer hits the stone
• Advantages: high crushing efficiency and low cost
• Typical applications: cement plants, building materials processing
1.5 Mobile crushing station (flexible crushing solution)
• Applicable scenarios: mines, construction waste recycling, temporary projects
• Advantages: no fixed installation required, can be quickly transferred to other sites
• Typical configuration: jaw crusher + cone crusher/impact crusher combination
2. How to choose the right marble crushing equipment?
2.1 Choose according to the hardness of the stone
• High-hardness stone (granite, basalt) → jaw crusher + cone crusher combination
• Medium-hardness stone (marble, limestone) → jaw crusher + impact crusher combination
• Low-hardness stone (shale, gypsum) → hammer crusher or impact crusher
2.2 Choose according to the particle size requirements of the finished product
• Coarse crushing (0-300mm) → jaw crusher
• Medium crushing (30-100mm) → cone crusher or impact crusher
• Fine crushing (0-30mm, sand making) → impact crusher (sand making machine)
2.3 Choose according to production capacity requirements
• Small production line (50-100 tons/hour) → single jaw crusher or impact crusher
• Medium-sized production line (100-500 tons/hour) → multi-stage crushing combination
• Large mine (more than 500 tons/hour) → fully automatic crushing and screening system
2.4 Environmental protection and energy saving requirements
• Choose low-noise equipment equipped with dust removal system
• Give priority to models with hydraulic adjustment and intelligent control to reduce energy consumption
3. Industry application of stone crushing equipment
3.1 Construction aggregate production
• Used for concrete and asphalt mixtures, requiring uniform particle shape and low powder content
• Recommended equipment: jaw crusher + cone crusher + sand making machine
3.2 Marble/granite slab processing
• Fine crushing is required to reduce stone waste
• Recommended equipment: jaw crusher + fine crushing impact crusher
3.3 Mining
• High-yield and wear-resistant equipment is required
• Recommended equipment: large jaw crusher + multi-cylinder hydraulic cone crusher
3.4 Construction waste recycling
• Mobile crushing station is required to achieve on-site crushing
• Recommended equipment: mobile jaw crusher + impact crusher combination
4. How to optimize the stone crushing production line?
• Reasonable configuration of crushing stages: avoid over-crushing and reduce energy consumption
• Choose wear-resistant accessories: high manganese steel jaw plate and composite alloy hammer head to extend equipment life
• Automatic control: use PLC intelligent system to improve operation stability
• Regular maintenance: check lubrication system and fasteners to reduce failure rate
When selecting marble crushing equipment and stone crushing equipment, it is necessary to comprehensively consider factors such as material characteristics, production capacity requirements, and finished product specifications. We provide a variety of equipment such as jaw crushers, cone crushers, impact crushers, etc., support customized production line solutions, and provide one-stop services such as technical guidance, installation and commissioning, and after-sales maintenance.
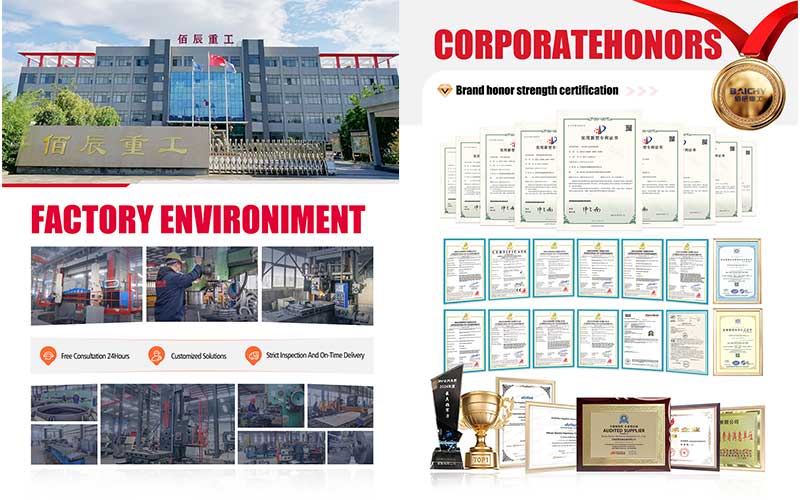
Baichy Heavy Industry – Your Trusted Partner for Seamless Equipment Operation
To ensure optimal performance of your equipment, Baichy Heavy Industry offers:
- Professional on-site installation guidance
- Comprehensive operator training
- 24/7 technical support & maintenance services
Our complete after-sales service system guarantees long-term, stable operation of your machinery with minimal downtime.
Protect Your Rights – Only Use Official Channels
To avoid scams and ensure authentic support, contact us exclusively through:
• Official Website: www.baichychina.com
• WhatsApp: +8615093222637
• Email: [email protected]
Your satisfaction is our priority – expect prompt, professional service every time.
(Note: Beware of unauthorized third parties claiming to represent Baichy. Always verify through official contacts.)
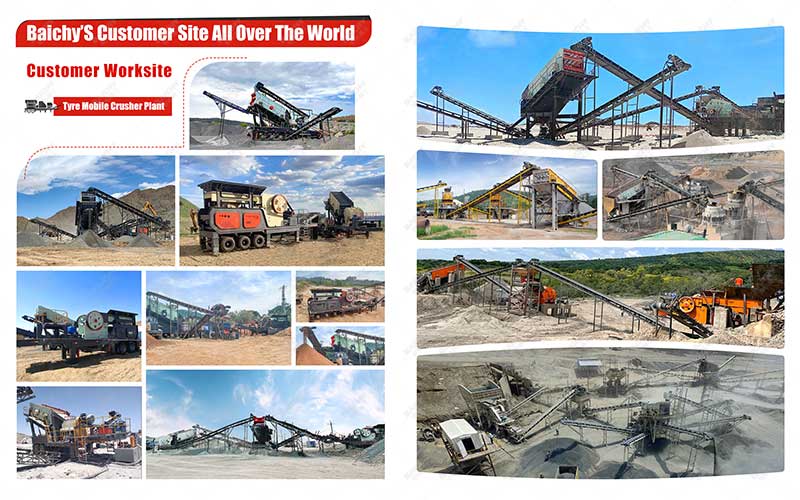