This case is an equipment configuration plan for a 1600t/h granite production line. After the project is completed, it can radiate to many surrounding areas. It has unique geographical advantages and can provide high-quality and sufficient construction sand and gravel aggregates for the region and surrounding areas. It will promote the rapid development of infrastructure projects in the region, and also provide demonstration effects for the construction of green mines and smart mines.
Overview of granite production line:
1. Design capacity: 1600t/h
2. Design concept and program advantages: This program integrates high efficiency, energy saving, environmental protection, safety, and other core concepts, combined with local sand and gravel market demand, raw material materials, and customer requirements for high-quality concrete, in order to meet the needs of major material customer groups ( Concrete mixing station, asphalt mixing station, dry-mixed mortar station, civil material, water-stabilized mixing station, etc.)
The crushing and screening line is designed with double production lines, and the single line production capacity can reach more than 800 tons/hour. Compared with the single production line, the double production line has the advantage of guaranteed production capacity and relatively low production cost. The double production line can adjust the production equipment according to the market sales situation, so as to Cost control when reaching high and low peak material consumption.
Introduction to the technological process scheme of the limestone production line:
Introduction to the process flow:
This granite crushing production line is independently designed by Baichy Heavy Industry. It is a ZSW1500x6000 vibrating feeder, two pe1200x2500 jaw crushers, four multi-cylinder hydraulic cone crushers HP500, and 4 set GZG1500 vibrating feeders and four GZG125 vibrating feeders. 3YK3080 vibrating screen 2 sets, YK1860 vibrating screen 2 sets The transfer pile is designed between the first crushing and the second crushing, which can realize the independent operation of the secondary crushing. When certain crushing equipment is overhauled and maintained, other crushing equipment can continue to operate, thereby improving the running time and operation efficiency of the equipment. At the same time, the differences in the production capacity of the crushing equipment at all levels are reconciled, so that the crushing equipment at all levels can operate at full load to the greatest extent, and the energy consumption is reduced to the maximum extent, so as to create an energy-saving mine.
The first part: ZSW1500x6000 vibrating feeder screens some of the materials first, then sieve 0-5mm and 5-250mm stones through two YK1860 single-layer vibrating screens, and then transports 5-250mm stones to the transfer silo by truck.
The second part: The discharge of two first-breaking jaw crushers pe1200x1500 is conveyed to the intermediate stockpile by two B1400 belt conveyors, and then four second-breaking cone crushers HP500 are conveyed by two B1400 belt conveyors. The discharge is vibrated by two 3YK3072 After sieving and screening, 0-5mm, 5-15mm, and 15-25mm are direct to the finished material pile, and the stone larger than 25mm is returned to the cone crusher.
Three, the project advantages:
1. In response to the country's promotion of green mine construction, the production line adopts workshop design, including a primary crushing workshop, semi-finished product silo workshop, secondary crushing workshop, fine crushing workshop, screening workshop, finished product silo workshop, and belt conveying between workshops. The machine is connected by suspension, the belt conveyor and maintenance walkway are fully enclosed, the roads in the factory are hardened, and greening is done on both sides of the road.
2. Environmental protection: A bag-type dust collector is used in the workshop to suppress dust, and a water spray system is arranged on the top of the workshop to cooperate with dust removal equipment to reduce dust so that the dust emission during the production process of the entire production line is within the range of environmental protection requirements.
3. Safety: The strong and weak currents are separated, the power distribution room and the control room are separated so that the operator is far away from the high-voltage power supply, and the safety accidents of electricity use are minimized.
4. Overhaul: Each equipment workshop is equipped with simple driving, which is convenient, fast, and safe to overhaul equipment.
5. An electric valve is set under the finished product silo, and a belt conveyor is set at the lower part to transport the finished materials of various specifications to the silo of each mixing station through the belt conveyor, so as to reduce the environmental pollution and cost caused by the loader and the use of the loader and realize the realization of the mixing station. process control.
6. Automatic loading system: A belt conveyor is designed under the four finished product silos, which can transport quantitative aggregates of various specifications to the automatic loading system to realize dust-free automatic loading.
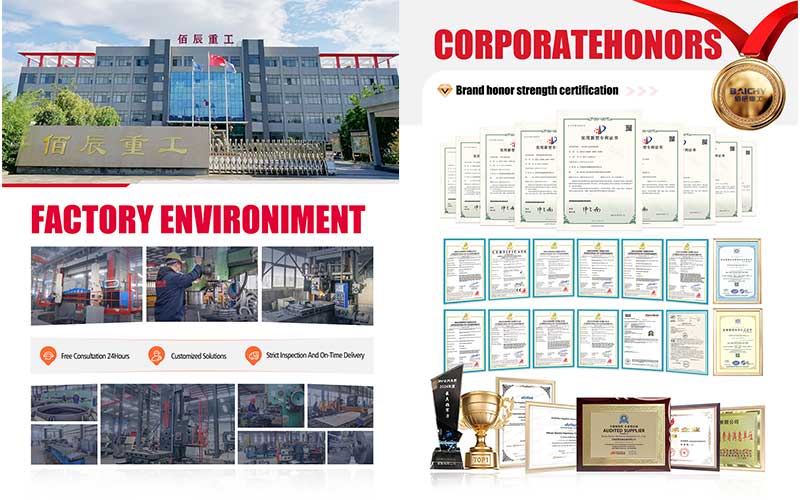
Baichy Heavy Industry – Your Trusted Partner for Seamless Equipment Operation
To ensure optimal performance of your equipment, Baichy Heavy Industry offers:
- Professional on-site installation guidance
- Comprehensive operator training
- 24/7 technical support & maintenance services
Our complete after-sales service system guarantees long-term, stable operation of your machinery with minimal downtime.
Protect Your Rights – Only Use Official Channels
To avoid scams and ensure authentic support, contact us exclusively through:
• Official Website: www.baichychina.com
• WhatsApp: +8615093222637
• Email: [email protected]
Your satisfaction is our priority – expect prompt, professional service every time.
(Note: Beware of unauthorized third parties claiming to represent Baichy. Always verify through official contacts.)
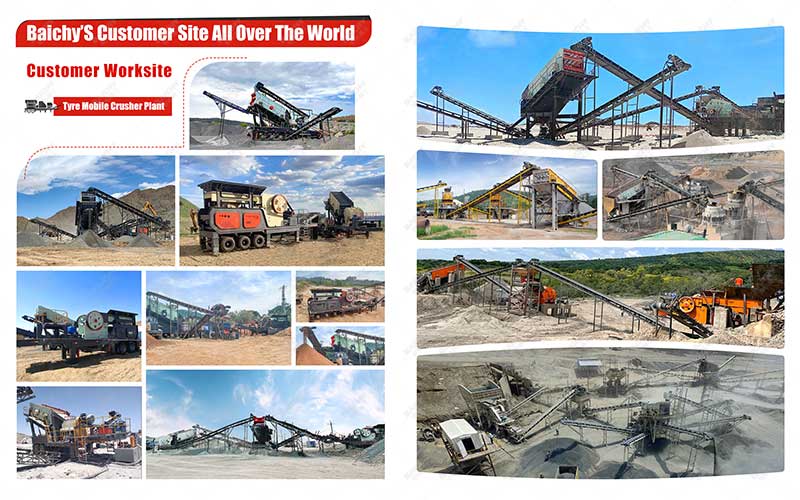