In the field of mining crushing, double-roll crusheris widely known for its advantages such as simple structure and precise particle size control. However, when faced with metal ores with high hardness and strong abrasiveness, many users will have questions: Can the double-roll crusher do the job? This article will combine the characteristics of metal ores, the working principle of the equipment and actual cases to give you a detailed answer.
1. Analysis of the applicability of double-roll crusher to metal ores
1.1 Types of metal ores that can be processed
Double-roll crusher is not completely unusable for metal ores, but its applicability is highly dependent on the hardness and abrasiveness of the ore:
• Metal ores suitable for crushing:
Low hardness ores: bauxite (Mohs hardness 2-3), pyrolusite, and some oxidized copper ores (such as malachite).
Medium and low abrasive ores: limonite after coarse crushing (compressive strength ≤80MPa).
• Ores that need to be used with caution or avoided:
High-hardness ores: magnetite (hardness 5.5-6.5), hematite, chalcopyrite, etc., which can easily cause rapid wear of the roller skin.
Highly abrasive ores: gold or copper ores containing quartz veins, which will significantly shorten the life of the equipment.
1.2 Key limiting factors
• Roller skin wear resistance: Even if high manganese steel or tungsten carbide composite roller skin is used, the replacement cycle may be as short as 1-2 weeks when continuously crushing high-hardness metal ores, and the maintenance cost will increase sharply.
• Capacity and efficiency: Metal ores are dense, and the processing capacity of the double-roll crusher may be only 30%-50% of that of the cone crusher with the same power.
2. Comparison of alternatives for metal ore crushing
If the double-roll crusher is not applicable, the following equipment combinations can be considered:
Equipment type | Applicable stage | Advantages | Disadvantages |
Jaw crusher | Coarse crushing | Handling large ore (≤1500mm) | Uneven discharge particle size (100-300mm) |
Cone crusher | Medium/fine crushing | Efficient crushing of high-hardness ores | Complex structure, high maintenance cost |
High-pressure roller mill | Fine/ultra-fine crushing | Energy-saving, suitable for extremely hard ores | High investment cost |
Recommended solution
• High-hardness metal ore: Jaw crusher (coarse crushing) → Cone crusher (medium crushing) → Ball mill (fine grinding).
• Low-hardness metal ore: Jaw crusher (coarse crushing) → Double-roll crusher (fine crushing to less than 10mm).
3. Methods to improve the applicability of double-roll crusher for metal ores
If double-roll crusher must be used, it can be optimized by the following measures:
31. Upgrade of wear-resistant materials:
Choose tungsten carbide (WC) or ceramic composite roller skin, the service life can be extended by more than 3 times.
3.2 Process adjustment:
Pre-screening to remove impurities such as quartz in the ore to reduce abrasiveness.
Reduce the feed particle size (such as crushing the ore to ≤50mm by jaw crusher before feeding it into roller crusher).
3.3 Equipment modification:
Install a hydraulic adjustment system to compensate for roller skin wear in real time and stabilize the discharge particle size.
4. Reference of actual application cases
Case 1: Bauxite fine crushing (an alumina plant)
• Ore characteristics: Mohs hardness 2.5, high viscosity.
• Equipment configuration: double-roll crusher (roller gap 3mm, nickel-chromium alloy roller skin).
• Effect: 80% of the discharge size is ≤5mm, the production capacity is 50t/h, and the roller skin life is up to 6 months.
Case 2: Gold-bearing quartz vein ore (failure lesson)
• Problem: The quartz content in the ore is >30%, resulting in severe wear of the high-chromium alloy roller skin within 10 days.
• Improvement: Switch to a cone crusher + ball mill combination, reducing costs by 40%.
Conclusion and Suggestions
Double-roll crusher can be used for crushing some metal ores, but the following conditions must be strictly met:
1. The ore hardness is ≤5 (Mohs hardness) and the abrasiveness is low;
2. Cooperate with coarse crushing equipment to control the feed size;
3. Use high-wear-resistant roller skin and make a maintenance plan.
Suggestions: Before selecting, be sure to conduct an ore crushability test and consult equipment manufacturers (such as FLSmidth and CITIC Heavy Industries) to obtain a customized solution.
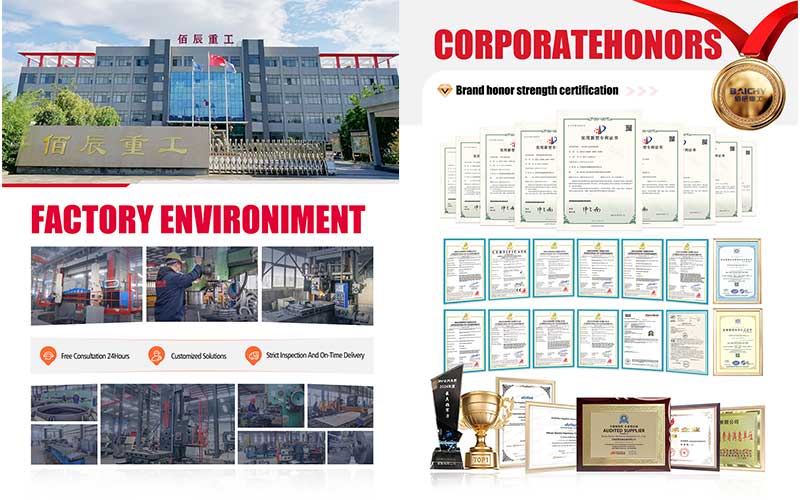
Baichy Heavy Industry – Your Trusted Partner for Seamless Equipment Operation
To ensure optimal performance of your equipment, Baichy Heavy Industry offers:
- Professional on-site installation guidance
- Comprehensive operator training
- 24/7 technical support & maintenance services
Our complete after-sales service system guarantees long-term, stable operation of your machinery with minimal downtime.
Protect Your Rights – Only Use Official Channels
To avoid scams and ensure authentic support, contact us exclusively through:
• Official Website: www.baichychina.com
• WhatsApp: +8615093222637
• Email: [email protected]
Your satisfaction is our priority – expect prompt, professional service every time.
(Note: Beware of unauthorized third parties claiming to represent Baichy. Always verify through official contacts.)
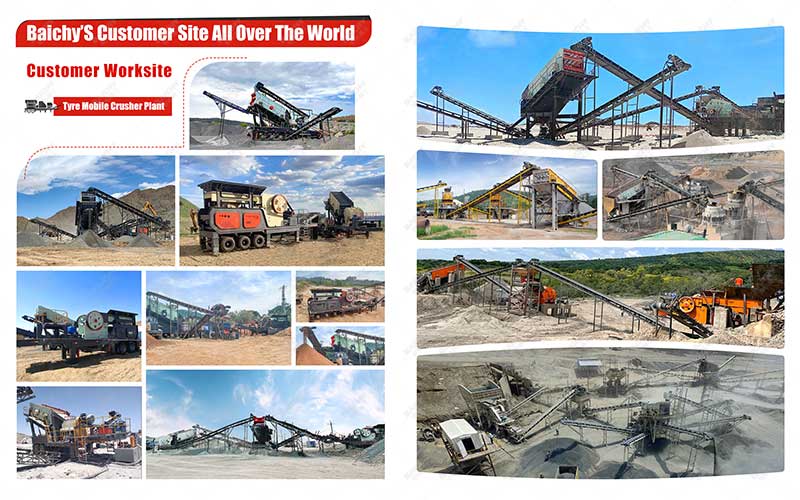