In the sand and gravel aggregate production industry, efficient and stable crushing production lines are the key to improving the production capacity and economic benefits of enterprises. The 300t/h aggregate crushing production line is an ideal choice for medium-sized sand and gravel plants, suitable for crushing hard rocks such as granite, limestone, and basalt. This article will combine the detailed flow chart to analyze the equipment configuration, process flow and core advantages of the production line to help users scientifically plan the layout of the production line.
1. Core equipment of 300t/h aggregate crushing production line
This production line usually adopts a combination of "jaw crusher + cone crusher + vibrating screen" to ensure high output and excellent finished product particle shape. The main equipment includes:
• Feeding equipment
Vibrating feeder (such as GZD series)
Function: Uniform feeding to prevent blockage of the coarse crusher.
• Coarse crushing equipment
Jaw crusher (such as PE-1200×1500)
The crushing ratio is large, suitable for primary crushing of large pieces of material.
• Medium and fine crushing equipment
Cone crusher (such as HPT300)
Suitable for medium and high hardness rocks, with better finished product particle shape.
• Screening equipment
Multi-layer vibrating screen (such as 3YK3070)
Achieve aggregate classification (0-5mm, 5-10mm, 10-20mm, etc.).
• Conveying system
Belt conveyor (B1000 type)
Connect various equipment to ensure smooth material transportation.
2. 300t/h aggregate crushing production line flow chart
Process flow description
• Feeding stage: The raw materials are evenly fed into the jaw crusher by the vibrating feeder.
• Coarse crushing stage: The jaw crusher crushes the large pieces of stone to ≤200mm.
• Medium and fine crushing stage: The cone crusher further crushes to ≤50mm to improve the qualified rate of finished products.
• Screening stage: The vibrating screen is classified by particle size, and unqualified materials are returned to the cone crusher for re-crushing (closed loop).
• Finished product output: Aggregates that meet the standards are transported to the finished product yard by conveyor.
3. Production line advantages
✅ High output and stable operation: 300 tons per hour, meeting the needs of medium-sized sand and gravel plants.
✅ Energy saving and environmental protection: The cone crusher adopts laminated crushing to reduce energy consumption by 30%.
✅ Automated control: PLC intelligent system reduces manual intervention.
✅ Strong adaptability: It can handle a variety of materials such as granite and river pebbles.
4. FAQ
Q1: How much space is required for a 300t/h production line?
A: It is recommended that the site length is ≥80m and the width is ≥50m, which needs to be adjusted according to the equipment layout.
Q2: What is the equipment investment cost?
A: Depending on the configuration, about 2-5 million (including auxiliary equipment).
Q3: What are the specifications of finished aggregates?
A: It can produce 0-5mm (machine-made sand), 5-10mm, 10-20mm, 20-31.5mm and other specifications.
This article analyzes the process flow and equipment configuration of the 300t/h aggregate crushing production line in detail, and attaches a high-definition flow chart to help users intuitively understand the operation logic of the production line. If you need a customized solution or equipment selection guidance, please contact us for professional support!
Consultation hotline: 0086 15093222637
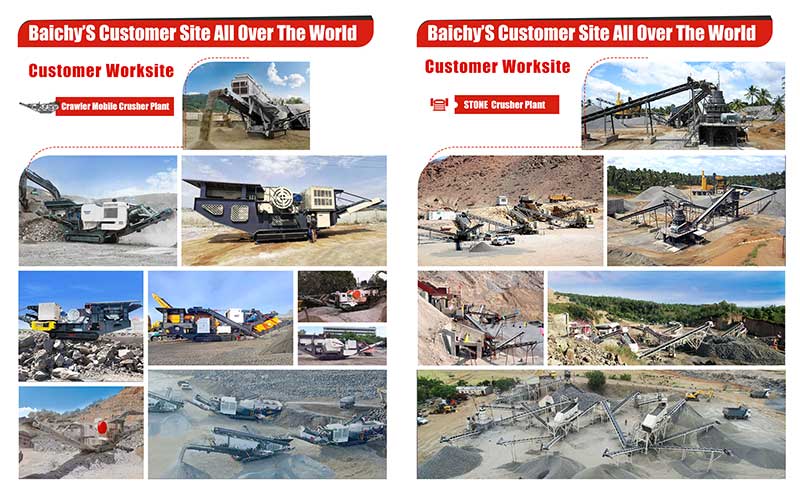