Vertical roller mill(VRM) is a highly efficient grinding machine that utilizes the vertical roller pressing principle. It is primarily used for crushing and grinding materials such as cement, slag, coal, and non-metallic minerals. Compared to traditional ball mills, VRMs offer significant advantages such as low energy consumption, high efficiency, a small footprint, and improved environmental performance. They have become mainstream equipment in the modern industrial grinding field.
1. Core Advantages of Vertical Grinding Mills
1. Energy Savings of 30%-50%: Energy consumption is significantly reduced compared to ball mills.
2. Small Footprint: The vertical structure design saves factory space.
3. High Grinding Efficiency: The material is directly crushed by rollers, and the fineness is adjustable.
4. Strong Drying Capacity: The material can be ground and dried simultaneously.
5. Environmentally Friendly and Low Noise: Smooth operation with minimal dust pollution.
2. Working Principle of Vertical Grinding Mills
Vertical Grinding Mills utilize a roller-pressing + air-classifying grinding method. The main process is as follows:
1. Feeding: The material enters the center of the grinding disc through an air-locked feeder.
2. Rolling and Crushing: The grinding rollers, under the action of a hydraulic system, apply high pressure to the material. The material is moved outward by centrifugal force and repeatedly crushed.
3. Classification and Separation: The crushed material is carried by a hot air stream into a classifier, where fine powder is collected and coarse powder is returned to the grinding disc for further grinding.
4. Finished product collection: Finished products that meet the fineness requirements are collected by cyclone separators or bag filters.
3. Applications of Vertical Grinding Mills
Due to their high efficiency and energy-saving grinding properties, vertical grinding mills are widely used in the cement industry (grinding raw materials, clinker, and slag), the metallurgical industry (micronizing solid wastes such as steel slag and slag), the power industry (preparing pulverized coal), and non-metallic mineral processing (ultrafine grinding of limestone, barite, and other minerals). They are essential core grinding equipment for modern chemical, building materials, and energy industries.
4. Key parameters
Parameters | Typical range/example |
Capacity | 5-300 t/h (cement raw material) |
Grinding disc diameter | 1.5-6.5 m |
Main motor power | 500-5000 kW |
Feed size | ≤5% greater than 50 mm (pre-crushing required) |
Finished product fineness |
300-500 m²/kg (specific surface area) |
5. Maintenance points
• Wear of grinding roller/grinding disc: repair by surfacing welding or replace wear-resistant lining.
• Hydraulic system: check oil pressure and sealing regularly.
• Bearing lubrication: special grease is required for high temperature conditions.
• Vibration monitoring: prevent vibration exceeding the standard due to unstable material layer or foreign matter.
6. Comparison of ball mill
Features | VRM | Ball mill |
Energy consumption | Low (~15 kWh/t) | High (~30 kWh/t) |
Noise | ≤85 dB | ≥100 dB |
Drying capacity | Synchronous drying is possible | Separate drying equipment is required |
Maintenance cost | High (many precision parts) | Low (simple structure) |
7. Development trend
• Intelligence: integrated sensors and AI to optimize operating parameters.
• Large-scale: single-machine capacity exceeds 600 t/h (such as cement raw material grinding).
• New Materials: Wear-resistant materials such as tungsten carbide extend component life.
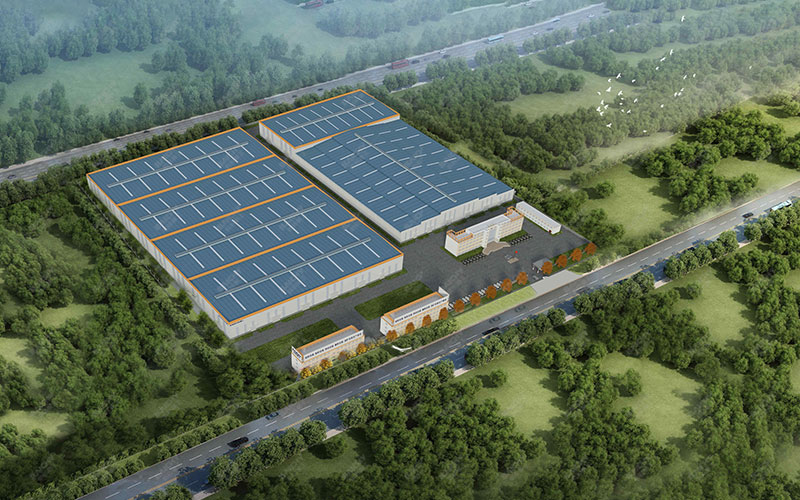
Baichy Heavy Industry – Your Trusted Partner for Seamless Equipment Operation
To ensure optimal performance of your equipment, Baichy Heavy Industry offers:
- Professional on-site installation guidance
- Comprehensive operator training
- 24/7 technical support & maintenance services
Our complete after-sales service system guarantees long-term, stable operation of your machinery with minimal downtime.
Protect Your Rights – Only Use Official Channels
To avoid scams and ensure authentic support, contact us exclusively through:
• Official Website: www.baichychina.com
• WhatsApp: +8615093222637
• Email: [email protected]
Your satisfaction is our priority – expect prompt, professional service every time.
(Note: Beware of unauthorized third parties claiming to represent Baichy. Always verify through official contacts.)
Further reading:
How To Choose A Suitable Industrial Grinding Mill?
Which Is Better Cement Vertical Roller Mill Or Ball Mill?
What Are the Differences between Dry and Wet Type Ball Mill?