Introduction of iron ore crusher
Iron ore crusher is a kind of equipment specially used for crushing raw iron ore step by step. It can crush large pieces of iron ore (usually about 500mm in size) into millimeter-level fine materials step by step.
Iron ore crushing material characteristics
Color and luster: Iron ore is usually a gray or brown mass with a hard texture and metallic luster.
Density: The density of different iron ores varies depending on their mineral composition and structure. For example, the density of magnetite is about 5.15, while the density of hematite is about 5.26.
Hardness: The hardness of iron ore also varies depending on its type, but it is generally hard.
Particle size: Iron ore exists in particles of different sizes in nature, but during the crushing and processing process, its particle size is adjusted to a size suitable for further processing.
Magnetite is a highly magnetic ore that can be easily separated using magnetic separation. Other types of iron ores, such as hematite, are not magnetic.
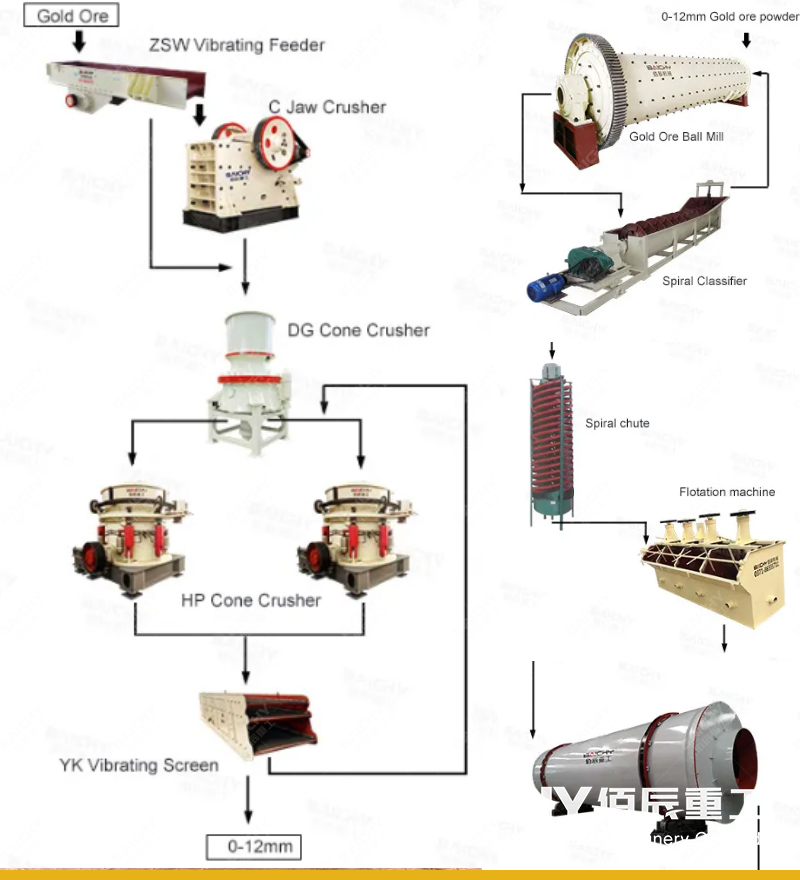
The crushing process of iron ore is a key step in iron ore processing and production. The following is a detailed introduction to the process:
1. Raw material preparation
The iron ore raw materials are initially screened to remove large impurities and obtain small pieces of iron ore suitable for crushing.
2. Crushing stage
Coarse crushing
Equipment: Use a jaw crusher or mobile jaw crushing station for coarse crushing.
Purpose: Crush large pieces of iron ore into larger particles for subsequent medium and fine crushing.
Medium crushing
Equipment: Single-cylinder hydraulic cone crusher for medium crushing.
Purpose: Further crush the coarsely crushed ore into smaller particles.
Fine crushing
Equipment: Multi-cylinder hydraulic cone crusher for fine crushing.
Purpose: Crush the medium-crushed ore into smaller particles to meet the requirements of subsequent processes.
3. Grinding stage
Equipment: Ball mill.
Process: The 0-12mm iron powder screened by the vibrating screen is evenly sent to the ball mill for grinding, and screened by the spiral classifier. Those that do not meet the requirements are sent to the ball mill for further grinding.
Purpose: To crush the iron ore into fine particles for subsequent beneficiation and smelting processes.
4. Magnetic separation stage
Equipment: Magnetic separator.
Process: The iron powder that meets the beneficiation requirements is sent to the magnetic separator for strong magnetic separation to remove impurities.
Purpose: To improve the recovery rate of iron ore.
5. Drying stage
Equipment: Dryer
Process: The obtained iron powder is sent to the dryer for drying.
Purpose: To remove moisture from the iron powder and obtain iron concentrate.
6. Screening and grading
During the crushing and grinding process, screening and grading are required. The iron ore that meets the requirements is sent to the production line for the next step of processing, and the iron ore that does not meet the requirements is returned to the previous stage for further crushing or grinding.
7. Finished product output
After the above process, the obtained iron concentrate is the finished product, which can be output through the conveyor.
Notes
During the crushing process, it is necessary to select appropriate crushing methods and process parameters according to the properties of the iron ore and the processing requirements to ensure the crushing effect and processing efficiency.
The dust pollution problem generated during the crushing process needs to be properly handled to reduce the impact on the environment and the human body.
The above is a detailed introduction to the iron ore crushing process, which is of great significance for improving the utilization rate and processing efficiency of iron ore.