As a representative of high-hardness rocks, granite is widely used in building aggregates, highway construction and large-scale infrastructure projects. However, its high compressive strength (usually 200-300MPa) and strong abrasiveness pose severe challenges to crushing equipment and processes. How to design a set of efficient granite crushing solutions with an output of 200 t/h? This article will deeply analyze the equipment selection, process flow and cost optimization strategy to help you build a cost-effective production line.
1. The core challenges of 200t/h granite crushing
• High hardness leads to fast equipment wear: Granite has a Mohs hardness of 6-7, and the life of traditional hammer crushers and impact crushers is short.
• Strict requirements for finished product particle shape: The aggregate market has high requirements for needle-like content (generally ≤15%), and the crushing process needs to be optimized.
• Environmental protection and energy consumption issues: Large-scale production lines need to take into account low noise and low dust emissions, while reducing the cost of electricity per ton.
Solution: Adopt "multi-stage crushing + laminated crushing" process, combined with intelligent control system, to achieve efficient and energy-saving production.
2. 200t/h granite crushing production line design
2.1 Equipment selection: jaw crusher + cone crusher + shaping sand making machine
Equipment type | Recommended model | Function | Advantages |
Coarse crushing | PE1200×1500 jaw crusher | Handling large granite (≤800mm feed) | High crushing ratio, wear resistance |
Medium crushing | HST315 single-cylinder hydraulic cone crusher | Secondary crushing to 50-80mm | Laminated crushing, excellent particle shape |
Fine crushing/shaping | VSI6X1145 impact sand making machine | Producing 0-5mm machine-made sand | The finished product has rounded particles and controllable powder content |
Auxiliary equipment | 3YK3070 vibrating screen, belt conveyor, dust removal system | Screening and grading, environmentally friendly dust reduction | Intelligent control |
Key points:
• Cone crusherreplaces impact crusher: granite crushing prefers hydraulic cone crusher, and the life of wear-resistant parts is increased by more than 50%.
• "Screen before crushing" process: pre-screening by vibrating screen reduces over-crushing and reduces energy consumption by 10%-15%.
2.2 Process optimization (with flow chart)
Three-stage closed-circuit crushing solution:
Coarse crushing stage: jaw crusher crushes the raw ore to ≤200mm.
Medium crushing stage: cone crusher further crushes, closed-circuit screening (screened material returns to cone crusher).
Sand making and shaping: impact crusher processes 5-30mm aggregate to produce high-quality machine-made sand.
Unique design:
• "Flexible adjustment" system: By hydraulically adjusting the cone crusher discharge port, 4-6 finished product specifications (such as 0-5mm, 5-10mm, 10-20mm) can be quickly switched.
• Dry dust removal + water mist dust suppression: Combined with pulse dust removal and spray dust suppression, dust emission ≤20mg/m³ (national standard requirement).
3. Cost and benefit analysis
3.1 1. Investment cost estimation (reference)
Project | Cost (RMB 10,000) |
Equipment procurement (jaw crusher + cone crusher + sand making machine) | RMB 350-450 |
Steel structure and conveying system | RMB 80-120 |
Electrical and intelligent control system | RMB 50-80 |
Environmental protection facilities (dust removal + noise reduction) | RMB 30-50 |
Total investment | RMB 5-7 million |
3.2 Operational economy
Power consumption per ton: 1.8-2.2kWh/t (15% lower than traditional solutions).
Wear-resistant parts cost: Cone crusher mortar wall life ≥6 months, ton crushing cost ≤2 yuan.
Payback period: Calculated based on the market price of granite aggregate 60-80 yuan/ton, 1.5-2 years to pay back.
4. Industry cutting-edge trends: intelligent and green crushing
• AI optimization system: real-time monitoring of equipment load through sensors, automatic adjustment of feeding speed, and avoidance of "idling" or "overloading".
• Zero-emission plant: wastewater recycling + photovoltaic power generation to create a carbon-neutral crushing production line.
• Mobile crushing solution: suitable for dispersed mining sites, modular design allows for rapid transfer (recommended 200t/h tire-type mobile station).
5. Conclusion: How to customize your 200t/h granite solution?
Key decision factors:
• Raw material characteristics (soil content, block size distribution)
• Finished product requirements (aggregate ratio, sand ratio requirements)
• Site restrictions (fixed/mobile selection)
Baichy Heavy Industry provides free on-site exploration + solution design to match the best equipment combination based on your actual needs. Consult now to get an exclusive configuration list and quotation!
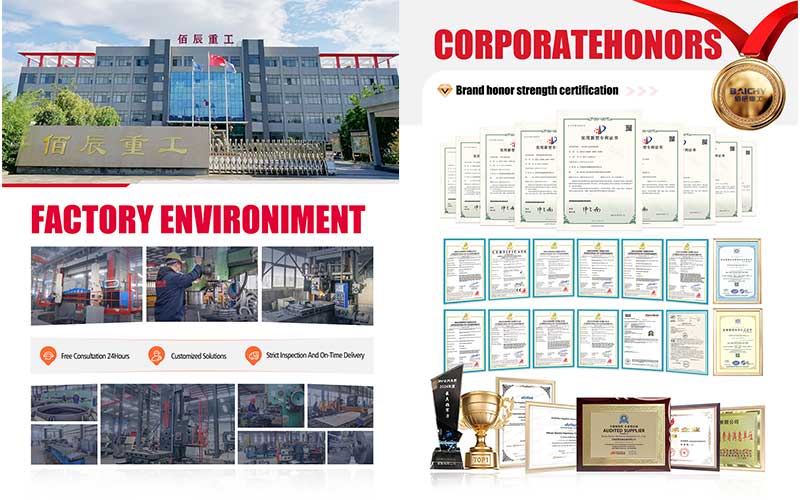
Baichy Heavy Industry – Your Trusted Partner for Seamless Equipment Operation
To ensure optimal performance of your equipment, Baichy Heavy Industry offers:
- Professional on-site installation guidance
- Comprehensive operator training
- 24/7 technical support & maintenance services
Our complete after-sales service system guarantees long-term, stable operation of your machinery with minimal downtime.
Protect Your Rights – Only Use Official Channels
To avoid scams and ensure authentic support, contact us exclusively through:
• Official Website: www.baichychina.com
• WhatsApp: +8615093222637
• Email: [email protected]
Your satisfaction is our priority – expect prompt, professional service every time.
(Note: Beware of unauthorized third parties claiming to represent Baichy. Always verify through official contacts.)
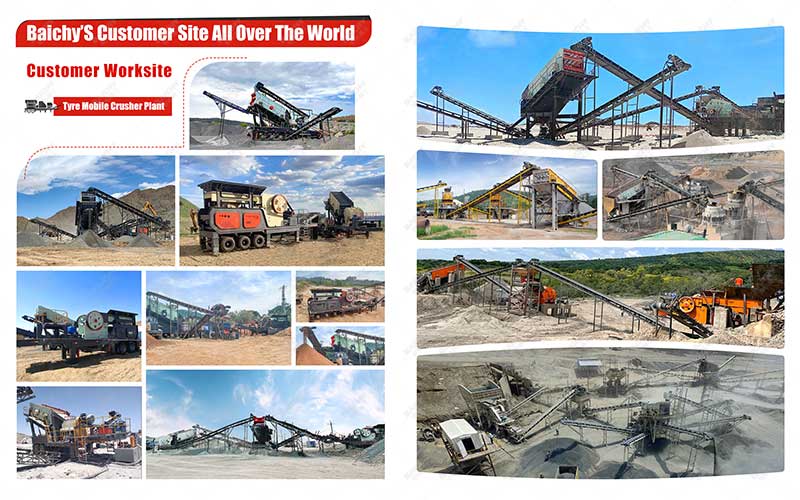