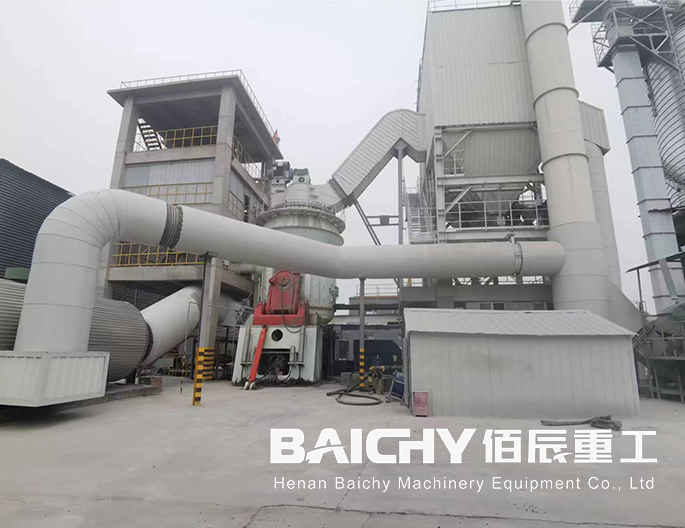
Vertical cement mills are particularly suitable for occasions that require large-scale grinding operations, such as cement production lines, building materials production lines, etc. When selecting a model, it is necessary to consider many factors such as production line scale, material properties, grinding power consumption, etc.
The vertical cement mill integrates multiple functions such as fine crushing, drying, grinding, powder selection, and transportation, which greatly simplifies the process flow and improves production efficiency. Due to the use of the material layer grinding principle, the vertical mill has low energy consumption during the grinding process, which is about 20%~30% more energy-saving than the traditional ball mill system. The vertical mill adopts a fully enclosed system, works under negative pressure, has no dust, and has a clean environment. At the same time, the dust collection device can effectively collect the dust-containing gas out of the mill to reduce pollution.
Model | Grinding table dia.(mm) | Max feeding size(mm) | Discharge size(um) | Discharge size(mesh) | Air-in tempreture(℃) | Air-out tempreture(℃) | Input material moisture | Final moisture | Capacity(t/h) | Motor Power(kw) |
---|---|---|---|---|---|---|---|---|---|---|
SRM1300 | 1300 | ≤38 | 212-45 | 70-325 | ≤350 | 70-95 | 4-15% | ≤1% | 10-35 | 185-250 |
SRM1500 | 1500 | ≤38 | 212-45 | 70-325 | ≤350 | 70-95 | 4-15% | ≤1% | 13-48 | 250-355 |
SRM1700 | 1300 | ≤38 | 212-45 | 70-325 | ≤350 | 70-95 | 4-15% | ≤1% | 18-68 | 355-600 |
SRM1900 | 1900 | ≤38 | 212-45 | 70-325 | ≤350 | 70-95 | 4-15% | ≤1% | 23-85 | 450-600 |
SRM2200 | 2200 | ≤38 | 212-45 | 70-325 | ≤350 | 70-95 | 4-15% | ≤1% | 36-135 | 710-1000 |
The SRM series vertical cement mill can completely replace the ball mill in cement production. The cement-specific surface area can reach 3800cm²/g, and the quality is stable and reliable.
According to actual measurement data of pulverized coal, vertical roller mills save more than 30% of energy per ton of cement clinker produced than traditional tube mills, and the energy-saving effect is very significant.
The whole machine has low vibration and noise, and the fully closed system equipment works under negative pressure with no dust spillage and complies with national environmental protection requirements. The cement vertical roller mill changes the working mechanism to reduce friction and improve service life.
The vertical cement mill is equipped with an automatic control system, which can achieve remote control and is easy to operate. In addition, by repairing the oil cylinder and flipping the boom, roller sleeves, liners, and other components can be replaced quickly and easily, reducing the company's downtime losses.
Have Any Questions!