In the mining crushing production line, the crushing process is generally divided into primary crushing, secondary crushing and tertiary crushing. When faced with these equipment, how should we choose?
General recommendation: For primary crushing (coarse crushing), jaw or gyratory crushers are preferred to handle large pieces of high-hardness materials; for secondary crushing (medium crushing), cone crushers (high hardness, high wear resistance) or impact crushers (medium and low hardness, excellent particle shape) are selected according to the hardness of the material; for tertiary crushing (fine crushing/shaping), vertical shaft impact crusher (sand making) or fine crushing cone crusher are recommended, taking into account the finished product particle shape and fineness.
In addition, these selections need to match the input/discharge size, production capacity, material characteristics, and investment budget to ensure efficient connection of each stage (such as jaw crusher + cone crusher + sand making machine combination), and give priority to energy saving, maintenance cost and environmental protection requirements. The following are the key points for staged selection:
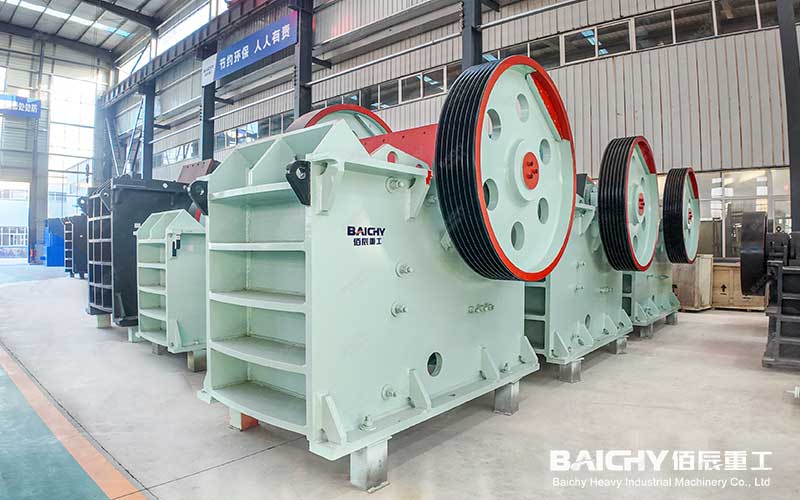
1. Primary crushing (coarse crushing)
Task: crush large pieces of raw ore (≤1500mm) to less than 250-300mm.
Equipment selection:
• Jaw crusher:
Advantages: simple structure, large processing capacity, suitable for hard materials (such as granite, basalt).
Applicable scenarios: mine head crushing, fixed production line.
• Gyratory crusher:
Advantages: continuous operation, larger processing capacity (up to 10,000 tons/hour), but high investment.
Applicable scenarios: large mines, high production requirements.
• Mobile jaw crusher:
Advantages: flexible transfer, suitable for temporary projects or dispersed operations.
Key parameters: feed size, compressive strength (recommended to select a jaw crusher for >250MPa), production capacity requirements.
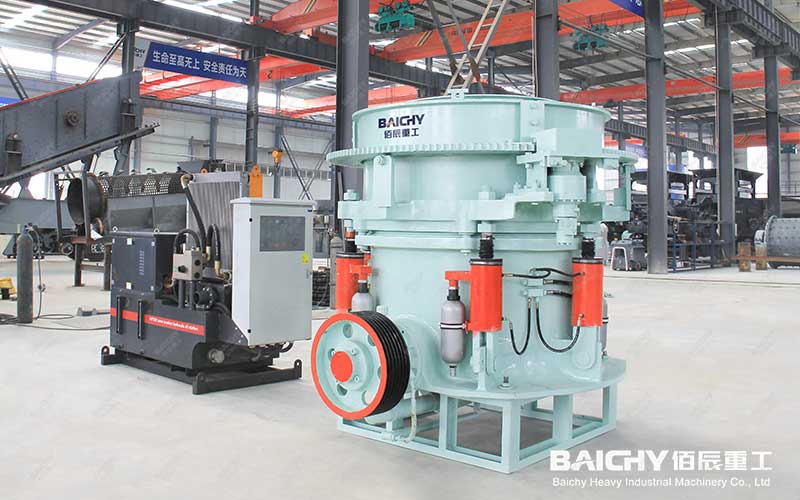
2. Secondary crushing (medium crushing)
Task: crush 250-300mm materials to 30-60mm.
Equipment selection:
• Cone crusher:
Advantages: strong wear resistance, suitable for medium and high hardness materials, good finished product particle shape (more cubes).
Type selection: single cylinder (simplified maintenance), multi-cylinder (high-precision adjustment).
• Impact crusher:
Advantages: large crushing ratio, good particle shape, suitable for medium and low hardness (such as limestone, coal gangue).
Note: The hammer wears quickly and needs to be replaced regularly.
• Mobile impact crusher:
Applicable scenarios: construction waste treatment, projects that require frequent transfer.
Key considerations: material hardness (such as Mohs hardness >5, cone crusher is preferred), particle shape requirements (aggregate production is preferred for impact crusher).
3. Tertiary crushing (fine crushing/shaping)
Task: crush 30-60mm materials to ≤10mm (or shape to 5-20mm high-quality aggregates).
Equipment selection:
• Vertical shaft impact crusher (sand making machine):
Advantages: efficient sand making, rounded grain shape, suitable for machine-made sand production.
Note: Impeller wear needs to be monitored, and the powder selector can adjust the powder content.
• High-pressure roller mill:
Advantages: energy saving, high fine powder output rate, suitable for ultra-fine crushing (such as iron ore tailings treatment).
• Fine crushing cone crusher:
• Applicable scenarios: fine crushing of high-hardness materials (such as basalt sand making).
• Key points: finished product use (concrete aggregates need good grain shape, and fillers can accept more powder).
Supplementary principles for selection
• Process matching: Ensure that the discharge size of each stage is connected (such as a combination of jaw crusher + cone crusher + sand making machine).
• Energy consumption and maintenance: Cone crusher has low energy consumption but complex maintenance, while impact crusher is the opposite.
• Environmental protection requirements: Closed design (such as dry process) reduces dust and is matched with dust removal equipment.
• Budget control: Small and medium-sized production lines can choose an impact crusher + sand making machine, and large projects prefer a cone crusher + vertical shaft crusher.
Example combination:
• Granite crushing: jaw crusher (primary) → multi-cylinder cone crusher (secondary) → vertical shaft sand making machine (third level).
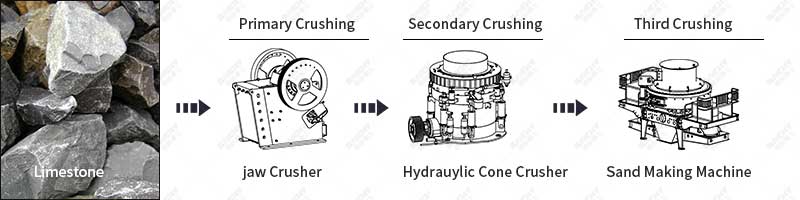
• Limestone crushing: jaw crusher (primary) → impact crusher (secondary) → shaping impact crusher (third level).