The following is a detailed design for a 100-150tph limestone crushing production line, covering equipment selection, process flow, investment budget and optimization suggestions, suitable for scenarios such as building aggregates and cement raw materials:
100-150tph limestone crushing production line core equipment selection and configuration
1. Primary crushing (coarse crushing)
- Jaw crusher: recommended model PE-750×1060 (processing capacity 100-200tph, feed size ≤630mm, discharge port adjustment range 80-140mm).
- Advantages: high crushing ratio, suitable for large pieces of limestone, simple structure and easy maintenance.
2. Secondary crushing (medium and fine crushing)
- Impact crusher (medium hardness limestone): recommended model PF-1315 (processing capacity 120-250tph, discharge size ≤40mm).
- Applicable scenarios: high requirements for finished product particle shape (such as building aggregates), but large wear-resistant parts loss.
- Cone crusher (high hardness or high silicon content limestone): Recommended model PYB1750 (processing capacity 150-350tph, discharge particle size ≤35mm).
- Advantages: strong wear resistance, suitable for long-term continuous production, but the particle shape is slightly inferior to the impact crusher.
3. Screening system
- Vibrating screen: Recommended 3YK2160 (three-layer screen, high screening efficiency), the screen hole size can be configured to 5mm, 15mm, 30mm, to meet the needs of various finished product specifications.
- Return material design: materials that do not meet the standards are returned to the secondary crusher through the belt conveyor to form a closed loop.
4. Auxiliary equipment
- Vibrating feeder: ZSW-490×110 (processing capacity 200-400tph), to ensure uniform feeding.
- Belt conveyor: bandwidth 800-1000mm, inclination ≤18°, with anti-deviation device.
- Dust removal system: pulse bag dust collector (air volume ≥ 20000m³/h), dust emission ≤ 20mg/m³.
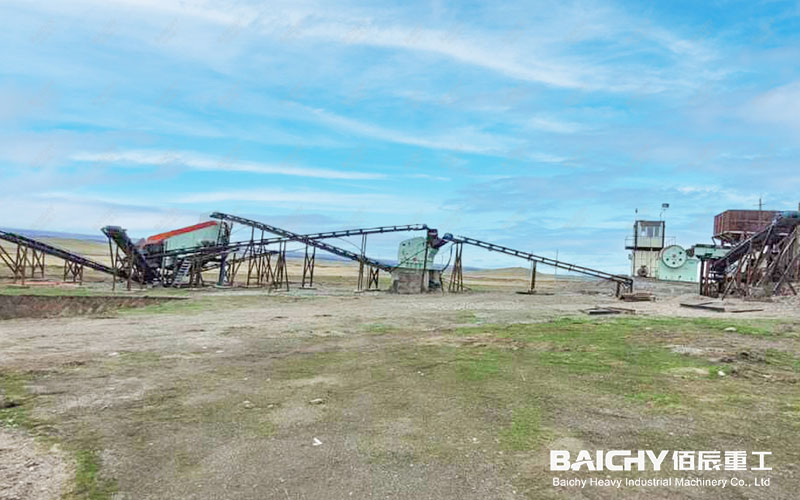
100-150tph limestone crushing production line process optimization
1. Three-stage one closed circuit design (high efficiency and energy saving)
Raw material warehouse → vibrating feeder → jaw crusher (coarse crushing) → impact crusher/cone crusher (medium and fine crushing) → vibrating screen → finished product (5-30mm)
- Advantages: closed-loop circulation reduces over-crushing and improves the yield of finished products by 10%-15%.
2. Flexible adjustment of finished product particle size
- Control the discharge particle size (for example: 5-10mm fine aggregate or 20-30mm coarse aggregate) by adjusting the gap between the impact crusher hammer or the distance between the cone crusher mortar walls.
3. Energy-saving measures
- Use variable frequency control of the vibrating feeder to match the crusher load and reduce no-load energy consumption.
- The cone crusher is equipped with a hydraulic system to achieve iron overload protection and stepless adjustment of the discharge port.
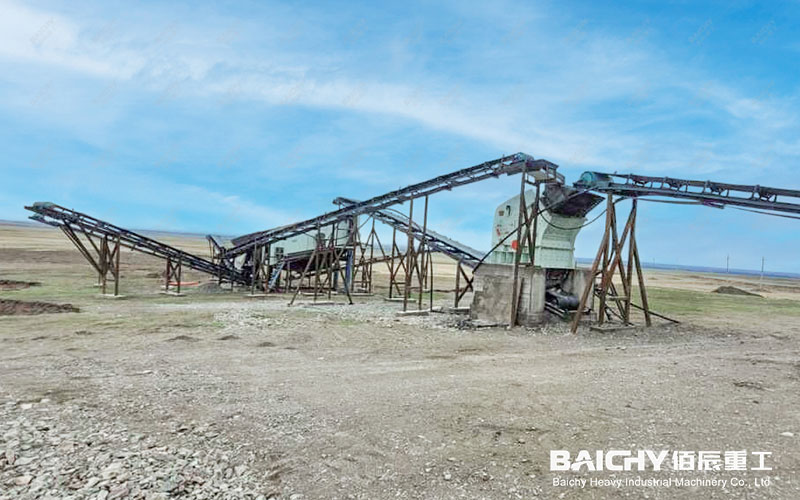
Key points for 100-150tph limestone crushing production line
1. Raw material control
- The water content of limestone is ≤10%, and the mud content is ≤5% to avoid clogging the screen and adhering to the crushing chamber.
- The maximum feed particle size is ≤ the allowable size of the jaw crusher (such as 750×1060 jaw crusher feed ≤630mm).
2. Equipment maintenance
- The jaw plate of the jaw crusher is replaced every 3-6 months, and the impact crusher hammer is checked for wear every 200-300 hours.
- The filter element of the cone crusher hydraulic system is replaced regularly to prevent oil circuit blockage.
3. Environmental compliance
- A spray device is configured to suppress dust, and the noise is controlled to ≤85dB (1 meter away from the equipment).
Case reference (production line of a cement plant)
- Configuration: PE750×1060 jaw crusher + PF1315 impact crusher + 3YK2160 vibrating screen.
- Capacity: stable 140tph, finished product size 0-5mm (30%), 5-15mm (40%), 15-30mm (30%).
- Power consumption: ≤1.2kWh/ton, annual operating cost of about 500,000 yuan.
The 100-150tph limestone crushing production line needs to select impact crusher or cone crusher according to the raw material characteristics (hardness, mud content) and finished product requirements (particle shape, grading). It is recommended to configure the automatic control system and efficient dust removal solution first to reduce operating costs and meet environmental protection requirements. Before investing, it is necessary to inspect the raw material mine on site and conduct a small test to determine the optimal crushing ratio and screening efficiency.