Grinding mills are essential equipment in mineral processing, cement production, and chemical industries. They break large pieces of ore into smaller particles for extraction or refinement. The most widely used mills are ball mills, SAG mills (semi-autogenous), and AG mills (autogenous grinding).
Choosing the right mill type is crucial for maximizing efficiency, reducing power consumption, and lowering operating costs. This guide explores their differences, working principles, advantages, and applications.
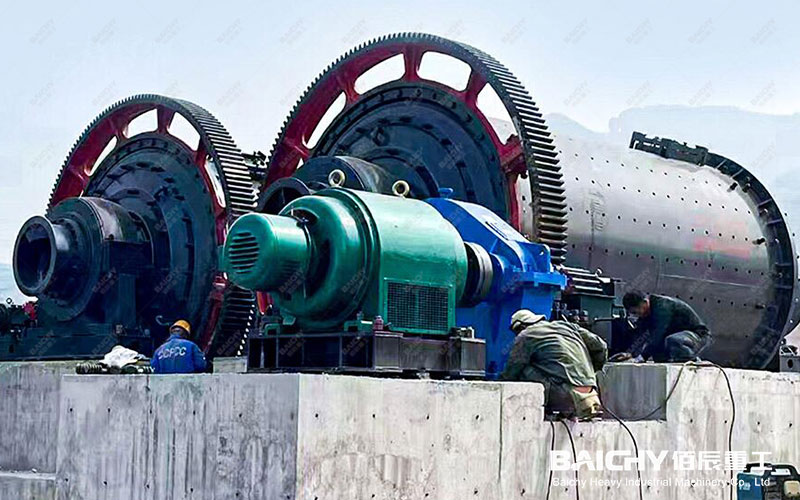
This is Ball Mill Project
1. What is a Ball Mill?
Principle of Operation
A ball mill is a rotating cylindrical machine filled with grinding media (steel or ceramic balls) that crush and grind materials into fine powder. As the mill rotates, balls are lifted and cascade, impacting the material for size reduction.
Types of Ball Mills
- Grid Discharge Ball Mill – Uses a discharge grid to retain coarse particles for further grinding.
- Overflow Ball Mill – Material exits through a hollow trunnion; ideal for fine grinding.
- Dry vs. Wet Grinding – Wet grinding (with water) is common in mineral processing; dry grinding is used in cement/chemical industries.
Applications
- Secondary/tertiary grinding (after crushers or SAG mills).
- Cement industry (fine clinker powder).
- Chemical/pharmaceutical industries (ultra-fine powders).
Advantages & Disadvantages
Advantages | Disadvantages |
Precise particle size control | High energy consumption (coarse) |
Wet/dry grinding compatible | Frequent media replacement |
Lower initial cost vs. SAG | Limited to smaller feed sizes |
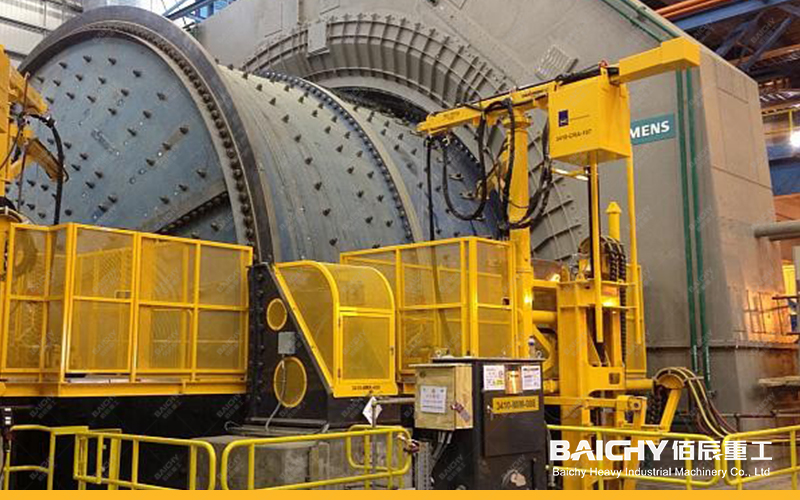
This is a SAG Mill Project
2. What is a SAG Mill?
Principle of Operation
A SAG mill uses ore (80–92%) + steel balls (8–15%) as grinding media. The ore self-breaks, while steel balls assist with harder particles.
Key Features
- Large diameter, short length (optimized for coarse grinding).
- Lifter plates for efficient cascading.
- Typically operates in closed circuit with ball mills.
Applications
- Primary grinding in mining (gold, copper, iron ore).
- Handles large feed sizes (up to 300 mm).
- Reduces need for secondary crushing.
Advantages & Disadvantages
Advantages | Disadvantages |
High throughput & efficiency | High liner/ball maintenance |
Handles large feed sizes | Complex control systems |
Fewer downstream stages | Higher operational costs |
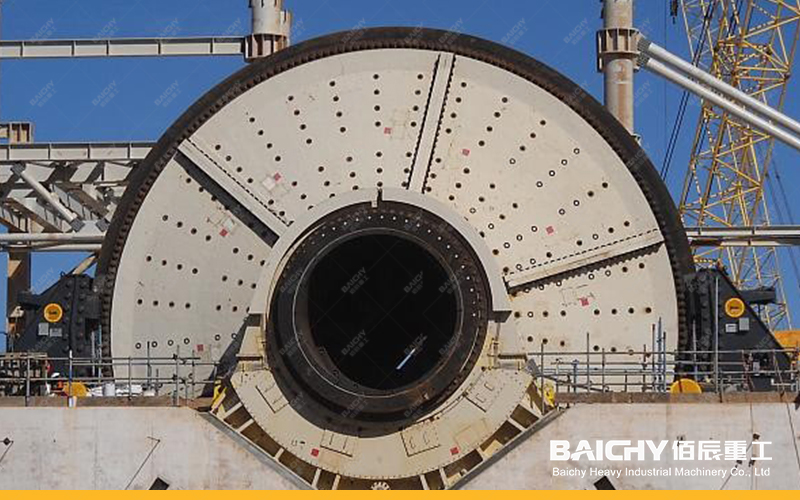
This is AG Mill Project
3. What is an AG Mill?
Principle of Operation
An AG mill relies solely on ore (no steel balls) for grinding via rock-on-rock impact.
Key Features
- No grinding media (lower costs).
- Simpler design (fewer moving parts).
- Requires larger mill size for equivalent output.
Applications
- Soft to medium, non-abrasive ores.
- Cost-sensitive operations (no steel ball expenses).
- Low-energy consumption scenarios.
Advantages & Disadvantages
Advantages | Disadvantages |
No steel ball costs | Limited to softer ores |
Low maintenance | Less efficient than SAG mills |
Simple operation | Larger mill size required |
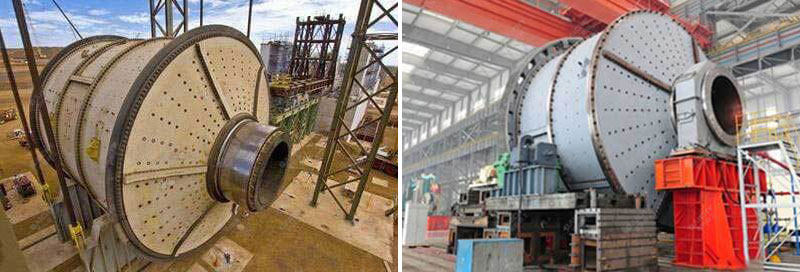
SAG Mill Vs. AG Mill
4. Key Differences Summary
Feature | Ball Mill | SAG Mill | AG Mill |
Grinding Media | Steel/ceramic balls | Ore + steel balls (8–15%) | Ore only |
Feed Size | Small (mm to microns) | Up to 300 mm | Up to 250 mm |
Efficiency | Best for fine grinding | Best for coarse grinding | Moderate |
Energy Use | High (fine grinding) | Lower per ton (coarse) | Moderate |
Maintenance | Medium (ball replacement) | High (liner wear) | Low |
Cost | Lower initial cost | Higher operational cost | Lower media cost |
Best For | Cement, chemicals | Hard ores (gold, copper) | Soft-medium ores |
5. How to Choose the Right Mill
1. Ore Characteristics
- Hard/abrasive ores → SAG Mill
- Soft-medium ores → AG Mill
- Fine grinding → *Ball Mill
2. Throughput Needs
- High-capacity mining → SAG Mill
- Smaller operations → AG/Ball Mill
3. Energy Efficiency
- SAG mills for coarse grinding.
- Ball mills for fine grinding (higher energy use).
4. Cost Considerations
- AG mills: Lowest media costs.
- SAG mills: Higher efficiency but more maintenance.
5. Hybrid Systems
- SAG + Ball Mill combos optimize large-scale mining.
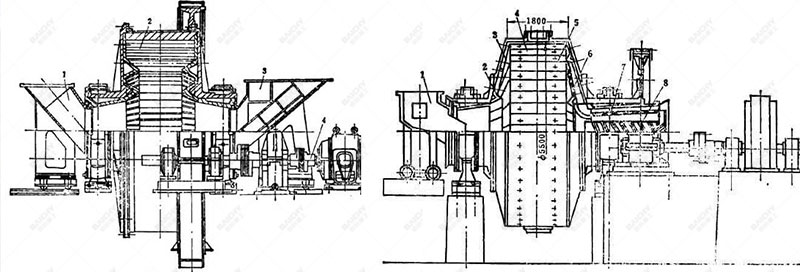
Dry type SAG Mill Vs. Wet type SAG Mill
6. Industry Applications
- Mining: SAG mills (gold/copper); AG mills (iron ore/phosphate).
- Cement/Chemicals: Ball mills dominate for fine grinding.
- Innovations: Advanced liners (e.g., FLSmidth, Weir) and automated controls.
7. Conclusion
- Ball Mill: Fine grinding (cement/chemicals).
- SAG Mill: Primary grinding (hard ores).
- AG Mill: Cost-effective for soft ores.
Optimization Tips:
Hybrid SAG + Ball Mill setups.
High-performance liners (e.g., rubber-metal hybrids).
Automated control systems.
8. Additional Resources
- Ball Mill Technical Guide – Selection tips.
Pro Tip: Consult grinding experts to match mill type to your ore and production goals!
Q&A: Ball Mill vs. SAG Mill vs. AG Mill
Q1: Main difference between ball mill and SAG mill?
A: Ball mills use steel balls; SAG mills use ore + balls. SAG excels in coarse grinding.
Q2: When to choose AG over SAG?
A: AG mills suit soft ores (e.g., limestone) where steel balls aren’t needed.
Q3: Best for gold ore?
A: SAG mill (primary) + ball mill (secondary) is most efficient.
Q4: SAG maintenance vs. ball mill?
A: SAG mills require more maintenance (liners, balls).
Q5: Best for cement?
A: Ball mills (or vertical roller mills for energy efficiency).