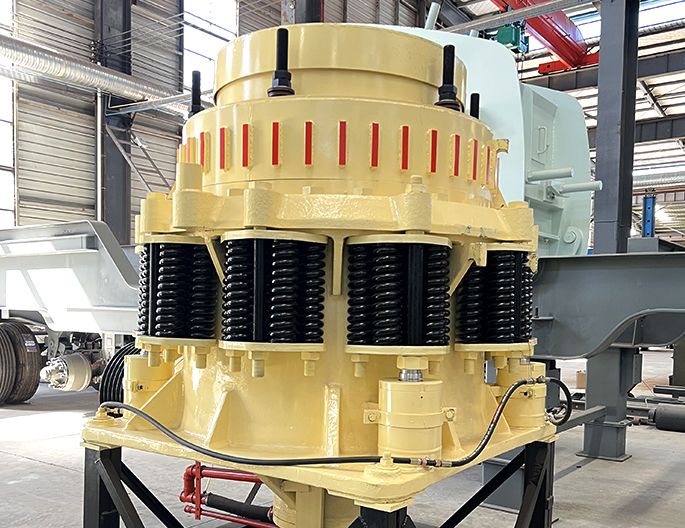
This crusher adopts the laminated crushing principle, which significantly increases the proportion of cubes in the product, reduces needle-like flake stones, and makes the particle size more uniform. This crushing method not only improves the crushing efficiency but also ensures the quality of the finished product.
Symons cone crusher adopts a large-diameter main shaft, a heavy-duty main frame, and an automatic control system with an independent thin oil lubrication system. These designs ensure the robustness and reliability of the equipment. In addition, its multi-point controlled independent thin oil lubrication system can ensure double protection of bearing lubrication and realize automatic safety protection of the entire machine.
Symons cone crusher has a variety of crushing cavity types, which can be selected according to different site conditions and needs. It can convert the cavity shapes of medium crushing and fine crushing and only needs to replace a few parts such as the corresponding cavity liner, making it more convenient to use one machine for multiple purposes. This enables the crusher to be widely used in various fields such as metal and non-metal mines, cement plants, building construction, sand making, and metallurgy.
All components of the Simons cone crusher can be disassembled from the top or side, making it easy to disassemble the fixed cone and move the cone assembly. In addition, bronze sliding bearings can maintain excellent load-bearing performance in high-impact, vibration, and crushing environments, and are more economical and easier to maintain than rolling bearings. These designs make equipment maintenance and upkeep easier and faster.
This crusher adopts advanced crushing technology and design concepts to minimize energy consumption and environmental pollution. Its efficient crushing method and optimized structural design greatly reduce noise, dust, and other pollutants generated by the equipment during operation, complying with modern environmental protection requirements.
Model | CS160-C | CS160-M | CS160-F |
---|---|---|---|
Crushing Cone Dia.(mm) | 1295(4 1/4') | 1295(4 1/4') | 1295(4 1/4') |
Adjusting Range of Discharge Opening(mm) | 19-51 | 16-38 | 13-31 |
Max feeding size (mm) | 205 | 178 | 115 |
Motor Power(kw) | 160 | 160 | 160 |
Capacity(t/h) | 172-349 | 132-253 | 109-181 |
Overall Dimension(mm) | 2983×1866×3156 | 2983×1866×3156 | 2983×1866×3156 |
NO. | Product Name | Model | Quantity |
---|---|---|---|
1 | Vibrating Feeder | ZSW9638 | 1 |
2 | Jaw Crusher | PE600x900 | 1 |
3 | Cone Crusher | CS160 | 1 |
4 | Cone Crusher | CS160 | 1 |
5 | Vibrating Screen | 4YK1860 | 1 |
6 | Belt Conveyor | B800 | 3 |
6 | Belt conveyor | B650 | 6 |
100-150t/h Granite crushing plant. Granite is a hard rock. It is a common stone material and is also a common building sandstone material. Granite is hard. When configuring the production line, it is necessary to fully consider the hardness of the rock and choose the appropriate equipment to be able to produce high efficiency and stability. crushing sand production line.
1. Coarse crushing module:Silo, vibrating feeder, jaw crusher, cs110 cone crusher;
2. Medium and fine crushing module:Silo, cs160 cone crusher, vibrating screen
3. Screening module:The screening module adopts a general-purpose circular vibrating screen, which is configured according to the requirements of the material. Generally, one set of sieves is sufficient for three types of materials, and two sets of sieves are required for 4-5 kinds of materials, which are configured according to the needs of customers.
Advantages of modular production lines
1. Modular design facilitates production management:Coarse crushing, medium and fine crushing, and screening are divided into modules to improve the utilization of site space and facilitate production management, even if the plant is built in the future, it will not be affected;
2. Accurate flow splitting and optimized crushing ratio:The coarse crushing module is equipped with a grate feeder, which can screen out some fine materials to avoid waste of jaw-crushing efficiency. This part of the fine materials will be conveyed to the vibrating screen through the belt for screening, and some crushed stones, muck, and crushed stones will be screened out. Part of it will flow into the bottom belt of the return crusher for sieving.
The output of the jaw crusher is first sent to the trench silo, which can effectively reduce the height of the entire granite crushing and sand-making production line, and at the same time solve the problem that the belt conveyor cannot be stretched due to the cramped site.
The feed of the CS cone crusher is the largest among all cone crushers, which further ensures that the capacity of the jaw crusher is fully released, and can optimize the crushing ratio task distribution of the primary crushing module and the secondary crushing module.
Thank you for your interest in Baichy Machinery. If you want to know more about our crushers and industrial grinding equipment.
Contact us now to find out what we can do for you!