Granite Stone Crusher Machine
To process granite into suitable particle sizes for application in different fields, appropriate crushing equipment is needed. Below Baichy Machinery introduces different types of granite stone crushers and how to choose the appropriate granite stone crusher.
For example, impact crushers and hammer crushers are not suitable for processing granite, so as to avoid the frequent replacement of subsequent worn parts that will delay production and increase costs.
Granite stone crushing machine can be divided into three categories according to the feed and product particle size: |
Coarse crusher |
1500~500mm |
350~100mm |
Medium crusher |
350~100mm |
100~40mm |
Fine crusher |
100~40mm |
30~10mm |
1. Coarse Crushing Equipment - Jaw Crusher
Jaw crusher is the most commonly used coarse crushing equipment. It is not only used for hard rocks such as granite but also basically for coarse crushing of soft and hard ores.
- • Advantages: simple structure, reliable operation, lightweight, low price, various models, small size, large feed port size (up to 1m), simple maintenance, and economical operation cost.
- • Disadvantages: The liner is easy to wear, the content of needle-like flakes in the product is high, and a vibrating feeder is generally required.
2. Coarse Crushing Equipment - Gyratory Crusher
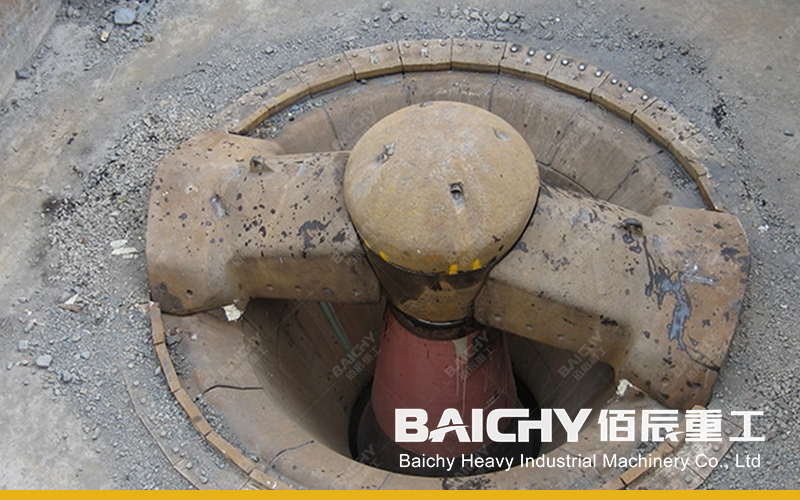
Gyratory crusher is also a commonly used coarse crushing equipment. Gyratory crusher is often used to crush materials of various hardness, but it is not suitable for crushing ores with high cohesiveness.
- • Advantages: Compared with jaw crusher, gyratory crusher belongs to continuous crushing. Its outstanding advantages are high production capacity, large crushing ratio, and can be fed with ore instead of direct feeding by the feeder.
- • Disadvantages: complex structure, high height, large volume, high requirements for factory buildings, large infrastructure investment, heavyweight, inconvenient transportation, and expensive.
3. Medium and fine crushing equipment - cone crusher
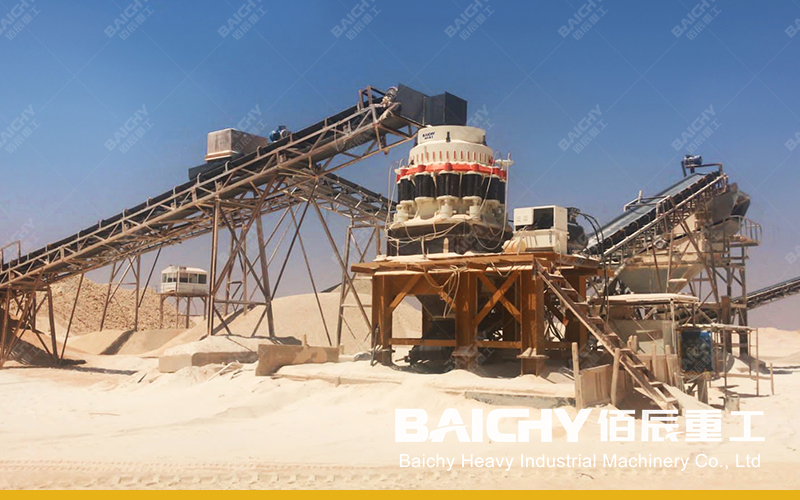
Cone crusher is definitely the most commonly used medium crushing equipment in the fine-crushing stage of granite. It has good wear resistance and many models, including spring type, Simmons type, single-cylinder hydraulic cone crusher, multi-cylinder hydraulic cone crusher, etc. However, the cone crusher is not suitable for crushing wet and highly cohesive ores.
- • Advantages: large crushing ratio, high efficiency, low energy consumption, less dust, uniform product particle size, stable operation, and low failure rate.
- • Disadvantages: complex structure and maintenance, high body, and expensive price.
4. Medium and fine crushing equipment - PEX fine jaw crusher
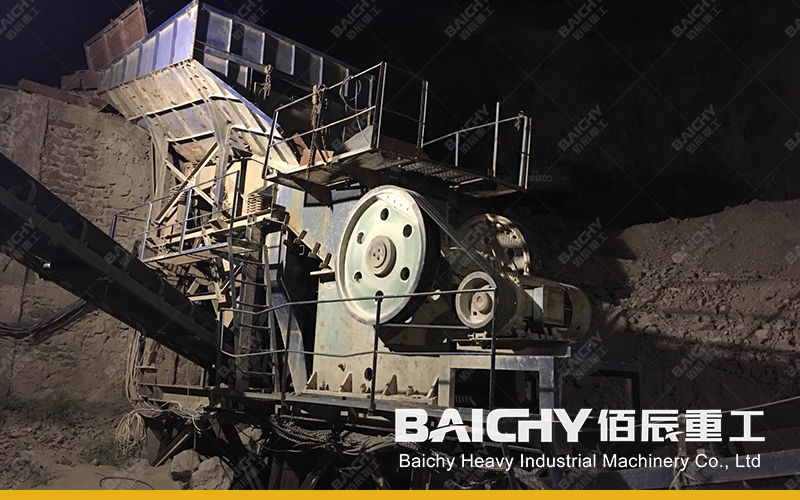
The structure and principle of the fine jaw crusher are similar to those of the jaw crusher. The material is crushed in the crushing chamber composed of the movable jaw and the fixed jaw, which can almost meet the requirements of various materials.
- • The PEX fine jaw crusher has a deep crushing chamber, no dead angle, a large crushing ratio, and a uniform product particle size, which can better meet the requirements of the sand-making process for fine crushing of raw materials.
- • Due to the optimized design of the crushing chamber, the PEX fine jaw crusher is not easy to block when processing materials, ensuring continuous and stable crushing operations and improving production efficiency.
5. Fine crushing equipment - vertical shaft impact crusher
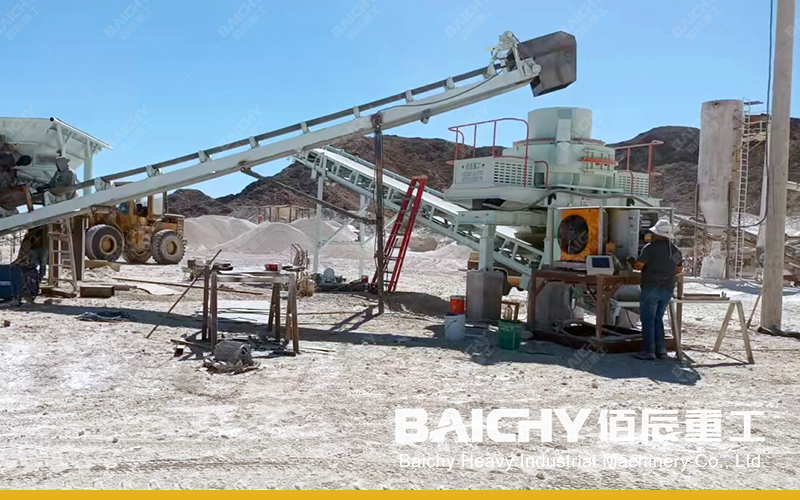
◆ If there is no strict requirement for the particle size of the product, cone crushers and fine jaw crushers can also be used in the fine crushing stage.
◆ If there is a strict requirement for the particle size of the product, a vertical shaft impact crusher is generally required for sand making and shaping.
Vertical shaft impact crushers can choose different crushing chamber types of "stone hitting stone" or "stone hitting iron". For granite, the hardness is relatively high, and it is not suitable to choose the "stone hitting iron" crushing chamber type, because the surrounding guard plates are easy to wear, the replacement is frequent, and the cost of wear-resistant parts is high.
- • Advantages: It has a shaping function, the product is cubic, and the volume is large. It is a widely used sand-making and shaping equipment on the market.
- • Disadvantages: Complex maintenance and high cost. Generally, the feed particle size of hard rock cannot exceed 45-50mm.
Granite crushing and sand-making plant
Due to the hard texture of granite, the crushing and sand-making plant is generally divided into three stages: coarse crushing, medium and fine crushing, and sand-making (shaping). The entire plant is mainly composed of vibrating feeders, jaw crushers, belt conveyors, cone crushers, vibrating screens, vertical shaft impact crushers, and sand washers.
The production process is as follows:
1. Coarse crushing stage
- • Coarse crushing equipment: The raw materials enter the jaw crusher for coarse crushing. With its powerful crushing capacity and stable performance, the jaw crusher has become the preferred head crushing equipment for the granite crushing production line.
- • Coarse crushing effect: After the coarse crushing of the jaw crusher, large pieces of granite are crushed into smaller particles, laying the foundation for subsequent medium and fine crushing operations.
2. Medium and fine crushing stage
- • Medium and fine crushing equipment: The coarsely crushed materials are transported to the cone crusher through a belt conveyor for medium and fine crushing. The cone crusher has become an ideal choice for the medium and fine crushing stages with its efficient crushing capacity and precise particle size control.
- • Medium and fine crushing effect: After the medium and fine crushing of the cone crusher, the material is further crushed into smaller particles to meet the feeding requirements of the sand-making machine.
3. Screening stage
- • Screening equipment: The medium and fine crushed materials enter the vibrating screen for screening. The vibrating screen classifies the materials according to the particle size through its vibration.
- • Screening effect: After screening, the materials that meet the requirements are sent to the sand-making machine for further processing, while the materials that do not meet the requirements are returned to the cone crusher for re-crushing.
4. Sand making stage
- • Sand-making equipment: The screened materials enter the sand-making machine for sand-making. The sand-making machine further crushes the materials and shapes them into sand particles that meet the requirements through its high-speed rotating impeller and impact plate.
- • Sand-making effect: After being processed by the sand-making machine, the materials are crushed into 0-5mm sand particles, meeting the standards for construction sand.
5. Sand washing stage
- • Sand washing equipment: The sand particles after sand making enter the sand washing machine for cleaning. The sand washing machine removes impurities such as soil and stone powder from the sand through its washing and screening functions.
- • Sand washing effect: After being washed by the sand washing machine, the sand becomes cleaner and purer, meeting the quality requirements of construction sand.
Baichy Machinery provides different types and models of the above-mentioned granite stone crushing machines for customers to choose from. And the engineers will recommend a suitable type and model for you according to the specific requirements. Chat with us if you need a granite stone-crushing machine!