The cement production line is a cement equipment production line composed of a series of equipment for producing cement. It mainly consists of processes such as crushing and pre-homogenization, raw meal preparation and homogenization, preheating and decomposition, cement clinker burning, cement grinding and packaging.
In the cement production process, raw material preparation is the first step. The main raw materials include limestone, clay, iron ore, etc. These raw materials need to be crushed and ground before they can be used in cement production. After the raw materials are mixed, they are sent to the rotary kiln for calcination to form clinker. Subsequently, the clinker is finely ground through a vertical roller mill, mixed with an appropriate amount of gypsum, and finally packaged through a packaging machine to become finished cement.
In the development process of the cement production line, it has experienced from the initial dry process stationary intermittent cylindrical natural ventilation ordinary shaft kiln, to the dry process horizontal rotary kiln with mechanized continuous production, and then to the birth and development of wet process cement manufacturing technology. The emergence of new dry process cement manufacturing technology and other stages. The new dry process cement production line has the advantages of energy saving, mature technology, low production cost and good production environment, but it also has the disadvantages of serious dust pollution, low production efficiency and high raw material requirements.
Currently, the cement industry is facing problems such as declining demand and overcapacity of clinker. It is predicted that cement production will continue to decline in the future, and the industry's surplus contradiction will become more acute. In this context, the optimization and upgrading of cement production lines is particularly important, through the introduction of advanced technology, improvement of production efficiency, reduction of energy consumption and reduction of pollution, to adapt to market demand and environmental protection requirements.
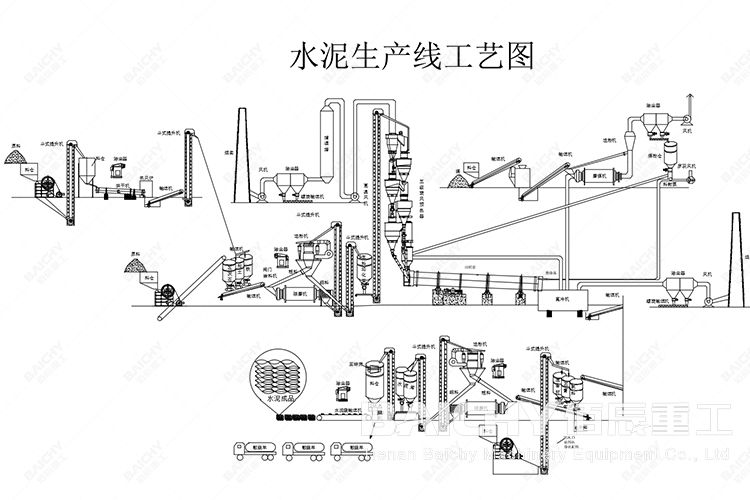
Cement production line process flow
1. Raw material preparation: This is the initial stage of cement production. The main raw materials include limestone, clay, iron ore, etc. These raw materials are generally obtained from mines and then transported to cement plants. In cement plants, these raw materials are crushed, ground, etc. to achieve the required particle size and composition.
2. Raw material mixing: The crushed and ground raw materials are mixed according to a predetermined ratio to ensure uniform cement composition.
3. Calcining: The mixed raw materials are sent to the rotary kiln for calcination. In the rotary kiln, raw materials are calcined at high temperatures (usually 1400-1500°C), causing chemical reactions to form clinker.
4. Clinker grinding: The calcined clinker is finely ground through a grinding mill to achieve the required particle size and surface area.
5. Cement preparation: The ground clinker is mixed and ground with an appropriate amount of gypsum to form cement. In this process, grinding is a key process, which is affected by many factors, such as the particle size, grindability, temperature, moisture, etc. of the material.
6. Packaging and leaving the factory: The prepared cement is sent to the packaging machine for packaging, or in bulk, and then transported to the finished product warehouse, and finally shipped out of the factory for sale.
Throughout the process, environmental protection treatment also needs to be considered, such as the treatment of waste gas, waste water, waste residue, etc., to ensure the environmental friendliness of production activities.
It is worth noting that the specific process flow may vary depending on factors such as the type of cement production line, equipment, raw materials, and production requirements. Therefore, in actual operation, the process flow needs to be adjusted and optimized according to specific conditions.